Advanced technology in plastic extrusion for modern industries
A Comprehensive Guide to the Process and Advantages of Plastic Extrusion
In the large world of manufacturing, plastic extrusion emerges as a vital and very efficient procedure. Altering raw plastic right into continual profiles, it provides to a huge selection of markets with its exceptional versatility.
Understanding the Basics of Plastic Extrusion
While it might show up complex initially glance, the process of plastic extrusion is basically straightforward - plastic extrusion. It is a high-volume manufacturing technique in which raw plastic is melted and shaped into a continuous profile. The process starts with the feeding of plastic material, in the form of granules, pellets, or powders, into a heated barrel. The plastic is after that melted using a mix of warmth and shear, applied by a revolving screw. As soon as the molten plastic reaches the end of the barrel, it is required via a small opening referred to as a die, shaping it right into a desired kind. The designed plastic is after that cooled down, strengthened, and cut right into preferred sizes, completing the procedure.
The Technical Refine of Plastic Extrusion Explained

Sorts Of Plastic Suitable for Extrusion
The option of the right type of plastic is a crucial facet of the extrusion process. Various plastics offer one-of-a-kind properties, making them much more matched to particular applications. Recognizing these plastic types can significantly improve the extrusion process.
Contrasting Plastic Extrusion to Other Plastic Forming Approaches
Recognizing the types of plastic ideal for extrusion paves the way for a more comprehensive discussion on how plastic extrusion piles up against other plastic forming approaches. Plastic extrusion is exceptional when it comes to creating continuous profiles, such as gaskets, seals, and pipelines. It likewise enables for a regular cross-section along the length of the item.
Key Advantages of Plastic Extrusion in Manufacturing
In the world of manufacturing, plastic extrusion offers lots of considerable advantages. One remarkable benefit is the cost-effectiveness of the process, which makes it a financially enticing production method. Furthermore, this strategy gives superior product flexibility and enhanced manufacturing speed, consequently increasing overall manufacturing performance.
Cost-efficient Manufacturing Method
Plastic extrusion jumps to the center as a cost-effective manufacturing approach in manufacturing. Furthermore, plastic extrusion needs much less power than conventional manufacturing approaches, adding to reduced operational costs. Generally, the economic benefits make plastic extrusion an extremely eye-catching choice in the manufacturing sector.
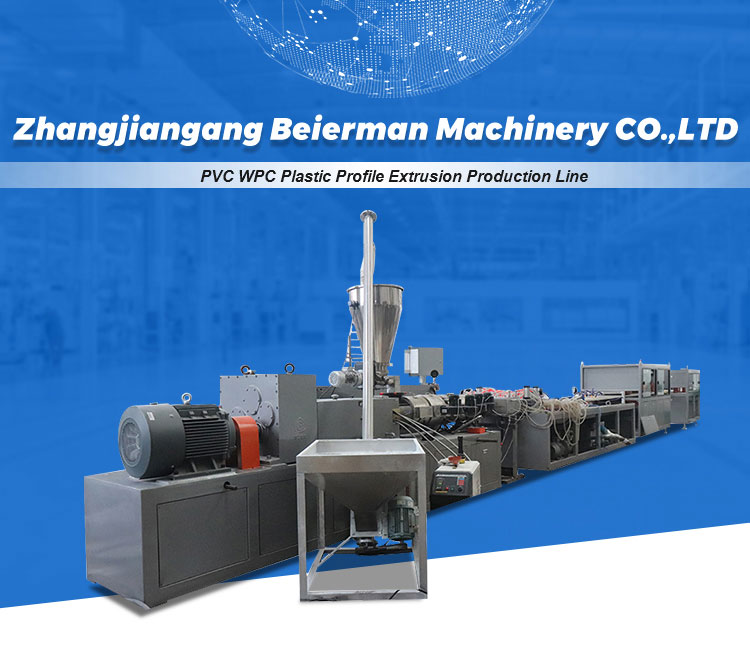
Superior Product Flexibility
Past the cost-effectiveness of plastic extrusion, an additional considerable advantage in manufacturing lies in its premium item versatility. This procedure enables the creation of a broad selection of products with differing shapes, designs, and dimensions, from straightforward plastic sheets to detailed profiles. The flexibility is associated to the extrusion die, which can be tailored to yield the preferred item style. This makes plastic extrusion an excellent remedy for markets that need customized plastic parts, such as vehicle, building, and packaging. The capability to produce diverse products is not just advantageous in conference specific market needs but additionally in enabling makers to check out new product with marginal capital expense. In significance, plastic extrusion's product adaptability promotes advancement while enhancing operational efficiency.
Improved Manufacturing Rate
A considerable advantage of plastic extrusion hinges on its enhanced production rate. This production process enables high-volume production in a reasonably brief time span. It can generating long, continuous plastic accounts, which substantially lowers the production time. This high-speed production is specifically beneficial in sectors where large amounts of plastic components are required within limited target dates. Few other production processes can match the rate of plastic extrusion. Additionally, the ability to preserve regular high-speed production without giving up item quality establishes plastic recommended you read extrusion in addition to various other approaches. The boosted manufacturing speed, therefore, not just makes it possible for producers to fulfill high-demand orders however likewise adds to boosted effectiveness and cost-effectiveness. This beneficial attribute of plastic extrusion has made it a favored option in various industries.
Real-world Applications and Influences of Plastic Extrusion
In the realm of production, the method of plastic extrusion holds extensive value. The economic advantage of plastic extrusion, mostly its high-volume and economical output, has changed manufacturing. The market is persistently aiming for technologies in naturally degradable and recyclable materials, indicating a future where the advantages of plastic extrusion can be kept without jeopardizing environmental sustainability.
Final thought
To conclude, plastic extrusion is a extremely effective and plastic extrusion effective technique of changing raw materials right into varied items. It uses numerous benefits over other plastic developing techniques, including cost-effectiveness, high output, minimal waste, and layout adaptability. Its influence is profoundly really felt in numerous industries such as building, auto, and durable goods, making it a pivotal process in today's manufacturing landscape.
Diving much deeper right into the technological procedure of plastic extrusion, it begins with the selection of the appropriate plastic material. When cooled, the plastic is reduced into the called for sizes or injury onto reels if the product is a plastic film or sheet - plastic extrusion. Contrasting Plastic Extrusion to Other Plastic Forming Methods
Understanding the kinds of plastic appropriate for extrusion leads the blog here means for a broader discussion on just how plastic extrusion piles up against other plastic forming methods. Couple of various other production processes can match the speed of plastic extrusion.